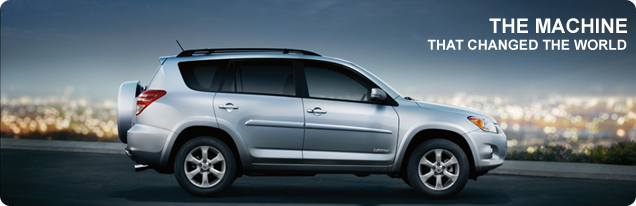
Introduction
• In cellular manufacturing, production work stations and equipment are arranged in a sequence that supports a smooth flow of materials and components through the production process with Minimal Transport or Delay.
• Implementation of this Lean Method often represents an attempt to combine the flexibility of a process layout with the efficiency of a product layout
• Rather than processing multiple parts before sending them on to the next machine or process step (as is the case in batch-and-queue, or large-lot production), cellular manufacturing aims to move products through the manufacturing process one-piece at a time, at a rate determined by customers' needs.
• The approach seeks to minimize the time it takes for a single product to flow through the entire production process.
• This One-Piece Flow method includes specific analytical techniques for assessing current operations and designing a new cell-based manufacturing layout that will shorten cycle times and changeover times.
• To make the cellular design work, an organization must often replace large, high volume production machines with small, flexible, "right-sized" machines to fit well in the cell.
• Equipment often must be modified to stop and signal when a cycle is complete or when problems occur, using a technique called Autonomation (or Jidoka).
• This transformation often shifts worker responsibilities from watching a single machine, to managing multiple machines in a production cell. (One-worker, multiple-machines) (OWMM)
• While plant-floor workers may need to feed or unload pieces at the beginning or end of the process sequence, they are generally freed to focus on implementing TPM and process improvements.
• Cellular manufacturing can also provide companies with the flexibility to vary product type or features on the production line in response to specific customer demands.
• Using this technique, production capacity can be incrementally increased or decreased by adding or removing production cells.
Characteristics
• Limited number of parts or models are processed with line flows.
• Based on the concept of group technology (GT), dissimilar machines are grouped into work centers, called cells, to process parts with similar shapes or processing requirements
• The layout of machines within each cell resembles a small assembly line
Group Technology
• Production Flow Analysis (PFA) is a group technology technique that reorders part routing matrices to identify families of parts with similar processing requirements
• The grouping into part families of items with similar design or manufacturing characteristics
Design characteristics: size, shape and function
Manufacturing or processing characteristics: type and sequence of operations required.
Advantages of cellular layout
• Reduced material handling and transit time
• Reduced setup time
• Reduced work-in-process inventory
• Better use of human resources:
Self-managed team, in most cases more satisfied with the work that they do
Flexible resource. Workers in each cell are multifunctional and can be assigned to different routes within a cell or between cells as demand volume changes.
• Easier to control
• Easier to automate
Disadvantages of a cellular layout
• Inadequate part families
Part families identified for design purposes may not be appropriate for manufacturing purposes.
• Poorly balanced cells
It is more difficult to balance the flow of work through a cell than a single-product assembly line, because items may follow different sequences through the cell that require different machines or processing times.
• Expanded training and scheduling of workers
Training workers to do different tasks is expensive and time-consuming and requires the workers' consent.
• Increased capital investment
Existing equipment may be too large to fit into cells or may be underutilized when placed in a single cell.
Additional machines of the same type may have to be purchased for different cells.
The cost and downtime required to move machines can also be high.
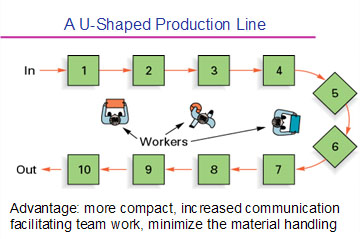
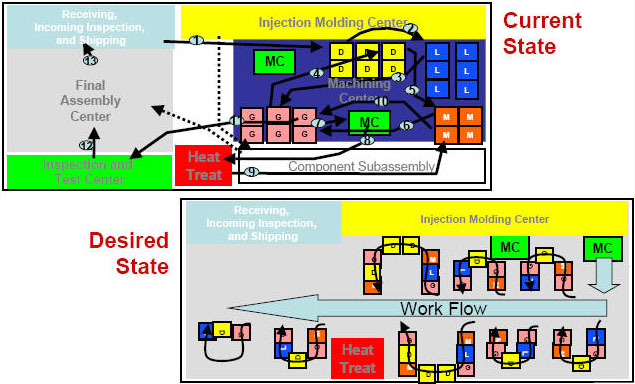
Conversion to cellular manufacturing
Step 1: Understanding the Current Conditions
• Assess the current work area conditions, starting with product and process data.
• PQ (product type/quantity) analysis is used to assess the current product mix.
• Document the layout and flow of the current processes using process route analyses and Value Stream Mapping (or process mapping)
• Measure time elements, including the cycle time for each operation and the lead time required to transport WIP between operations.
• Takt time, or the number of units each operation can produce in a given time, is another important time element to assess.
• Time elements are typically recorded on worksheets that graphically display the relationship between manual work time, machine work time, and operator movement time for each step in an operation.
Step 2: Converting to a Process-based Layout.
• Convert the production area to a cellular layout by rearranging the process elements so that processing steps of different types are conducted immediately adjacent to each other.
• For example, machines are usually placed in U or C shape to decrease the operator's movement, and they are placed close together with room for only a minimal quantity of WIP.
• The process flow is often counter clockwise to maximize right hand maneuvers of operators.
• To enable a smooth conversion, it is typically necessary to evaluate the machines, equipment, and workstations for movability and adaptability, then develop a conversion plan.
• In many cases, it is helpful to mock-up a single manufacturing cell to assess its feasibility and performance.
• Several techniques are important to facilitate effective cellular layout design and production.
SMED. Single-minute exchange of die to quickly convert a machine or process to produce a different product type. A single cell and set of tools can therefore produce a variety of products without the time consuming equipment changeover and set-up time to quickly respond to changes in customer demand.
Autonomation. Machines are able to stop, start, load, and unload automatically. In many cases, machines can also be designed to detect the production of a defective part, stop themselves, and signal for help. This concept has also been known as "automation with a human touch" and jidoka. This enabled one operator to manage many machines without risk of producing vast amounts of defective products. This technique is closely linked to mistake-proofing, or poka-yoke
Right-sized equipment. the replacement of large equipment with smaller equipment (not more than three times larger than the part they produce). Right-sized equipment is often mobile, so that it can quickly be reconfigured into a different cellular layout in a different location.
• Document new procedures for the new layout and train workers on the new production process.
• In many cases, workers from the affected processes participate in the conversion process.
• The new layout is also tested and measured against the baselines recorded in step 1 to confirm improvement.
Step 3: Continuously Improving the Process.
• Kaizen, TPM, and Six Sigma are commonly used as continuous improvement tools for reducing equipment-related losses such as downtime, speed reduction, and defects by stabilizing and improving equipment conditions
• Production Preparation Process (3P) is used to pursue a more systemic redesign of a production process to make a "quantum leap" with regard to production efficiencies and performance.
» More Information